Up to 40% of the total expense of an EV is attributed to the battery itself. A significant portion of this cost is directly related to the pace of development and the duration it takes to introduce the vehicle to the market.
Starting from the initial phases of battery development, assessing and characterizing battery components is critically important. Highly precise measurement techniques with fully automatized workflows, allow for rapid screening and provide inputs for creation of accurate high fidelity cell simulation models. Simulation models enable early design decisions during the development lifecycle, effectively frontloading the process and promoting key performance indicators (KPIs).
Design principles such as the commonization, consolidation, and deletion of components directly affect development time and cost. Design for manufacturability (DFM) as well as design for serviceability and recyclability also have an inpact on cost. These strategies will be supported by the next generation of flexible battery management system (BMS). Combined with simulation models, these resources will facilitate innovation while reducing complexity and overall costs by allowing engineers to evaluate different components including various cell technologies.
Join this session at the Fall Virtual Conference on EV Engineering, presented by AVL, to learn how modeling and validation with highly accurate tests on next generation of hardware enables conceptual flexibility, minimal time to market, and competitive confidence.
Key Takeaways:
- Addressing the time to market challenge is crucial in battery development
- AVL’s combined capabilities of testing, simulating, and engineering enables rapid and confident development
- Cost reduction strategies and viable production intent solutions are obtainable with a flexible BMS
Other sessions at our Fall Virtual Conference include:
The Fundamentals to Master Battery Validation and Production and the Challenges Ahead
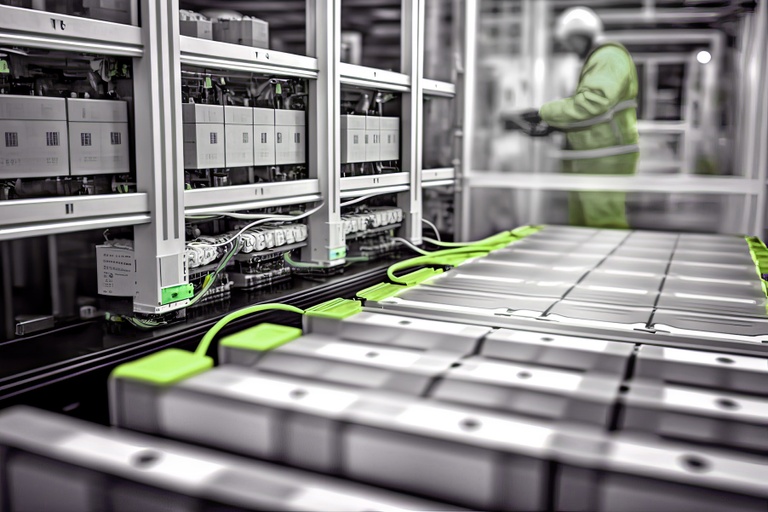
The battery market for e-Mobility continues to grow, despite limited resources and challenging supply chains. As a result, competition is increasing and sustainable battery manufacturing is no longer a fashionable trend, but an absolute must in order to survive in the industry.
In addition to optimizing factory infrastructure and manufacturing processes, companies require end-to-end quality assurance from the cell to the finished battery.
Join this webinar, presented by Averna, to explore how these aspects can be combined to achieve sustainability in battery production. Join our experts as they review:
- Managing time-sensitive deadlines.
- The parallel development of a product and its test system.
- Test expertise vs battery expertise.
- Interfaces to existing data analytics and processes.
- Future-proofing a test solution for unknown requirements.
See the full session list for the Fall Virtual Conference on EV Engineering here.

Broadcast live on October 2 – 5, 2023, the conference content will span the EV engineering supply chain and ecosystem, including motor and power electronics design and manufacturing, cell development, battery systems, testing, powertrains, thermal management, circuit protection, wire and cable, EMI/EMC and more.