Battery recycler Aqua Metals has demonstrated the recovery of high-purity lithium hydroxide from lithium-ion battery black mass at the company’s Li AquaRefining recycling facility in Nevada.
“The production and availability of the first recycled lithium hydroxide at scale will help close the supply chain loop for critical battery metals in America, paving the way for a more sustainable, efficient battery manufacturing industry,” says the company. “The immediate recovery of lithium hydroxide also improves the economics of recycling advanced battery chemistries like lithium iron phosphate (LFP), in which lithium makes up most of the valuable material, unlike nickel and cobalt-based batteries.”
Aqua Metals’ Li AquaRefining pilot facility is a closed-loop recycling system that’s designed to recover all the critical resources contained in spent batteries primarily using electricity, without the polluting furnaces or intensive chemical processes typical of recycling. Aqua Metals plans to produce battery-grade lithium hydroxide directly from black mass using its patent-pending, regenerative electro-hydrometallurgy process.
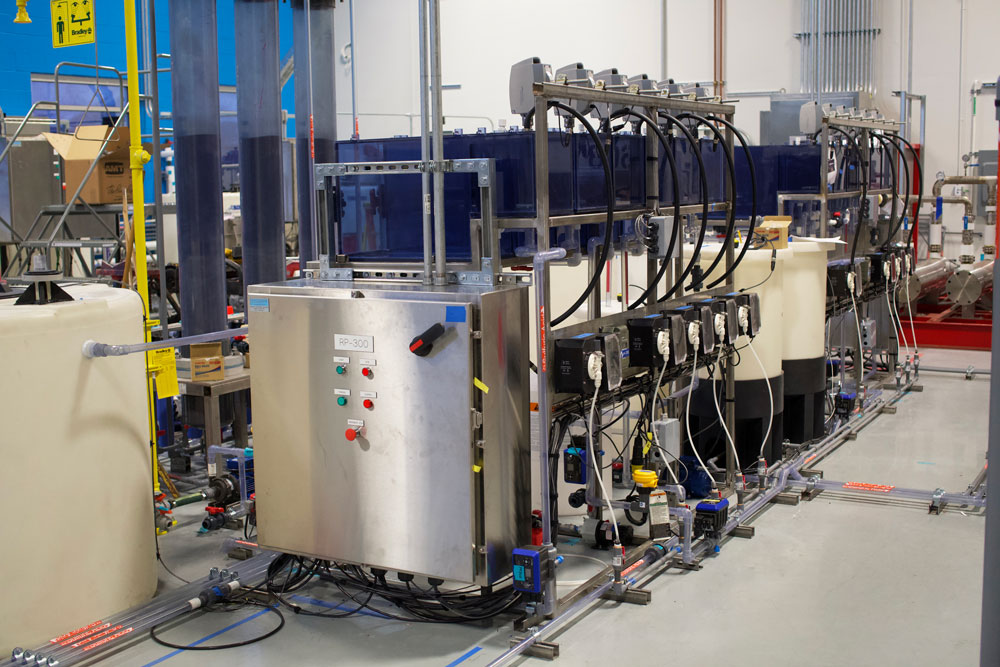
The pilot facility is designed to recover lithium hydroxide and manganese dioxide, as well as pure cobalt, nickel, and copper metals, from spent lithium-ion batteries, and provides the design basis for the company’s 10,000-ton-per-year recycling campus, which is planned for phased development starting later this year.
“We believe Li AquaRefining is now the only proven battery recycling technology that can produce lithium hydroxide at scale—avoiding the need for additional costly and polluting refinement,” said CEO and President Steve Cotton. “This new capability can have a profound impact on the lithium battery industry in North America. Our sustainably recycled lithium can help ensure a robust supply of critical metals to meet the Inflation Reduction Act’s ambitious goals for domestic content, and enables us to share samples and advance our discussions with prospective partners in battery and cathode manufacturing.”
“Successfully scaling up our unique lithium hydroxide recovery process is a major technical milestone for the industry, heralding an era of low-emissions, circular supply of critical battery metals produced from domestic resources,” said Chief Engineering and Operations Officer Ben Taecker. “Producing large quantities of recycled feedstock is new to battery manufacturing, and our ability to combine the recycling and refining of lithium into one process avoids unnecessary waste streams, lowers overall costs and improves supply chain efficiency.”
Source: Aqua Metals