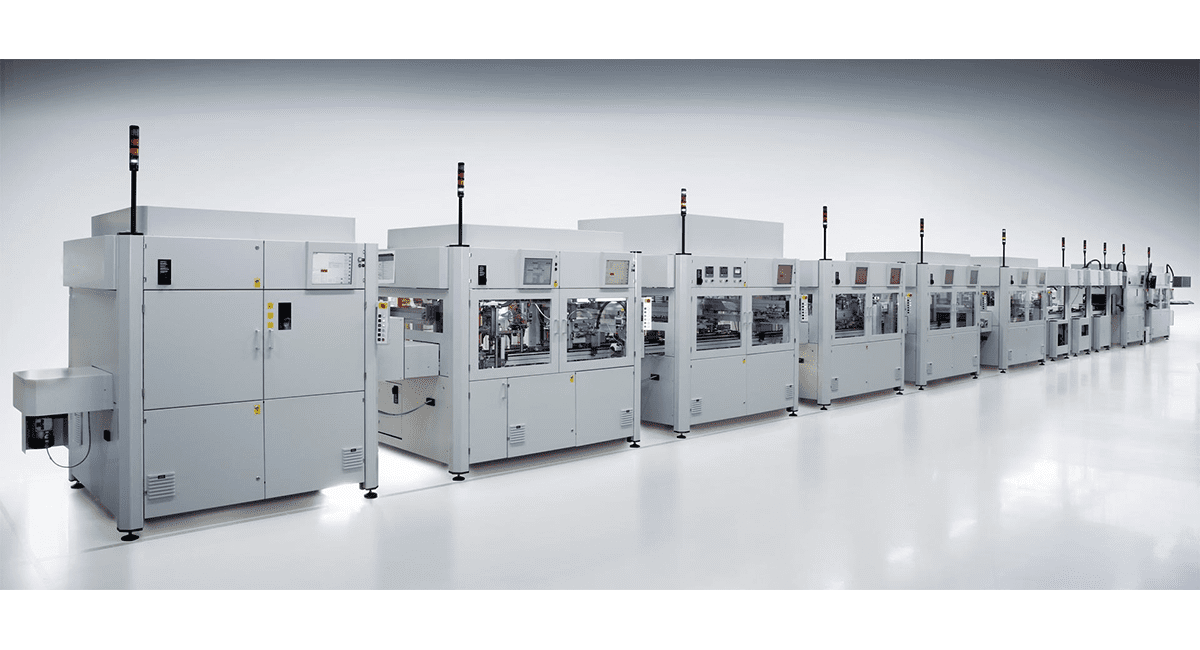
Sponsored by Schuler.
After acquiring the Italian Sovema Group, Schuler is gradually establishing itself as a system supplier in the field of battery production. The first successful large-scale projects show that the strategy is working.
Schuler passed an important milestone as a supplier for gigafactories with the construction of a formation line for a large German battery cell manufacturer. After the planned start of production in May 2025, the line will be able to produce around 80 cylindrical lithium-ion cells per minute. In addition to planning, manufacturing, and assembling the line, Schuler has also taken on the entire intralogistics, the steel construction, and the implementation of digital solutions that include a track-and-trace functionality for the plant.
The increasing business activity, that Schuler has only recently developed for the production areas of cell assembly and formation, follows a clearly defined strategy. The ANDRITZ Group, as the parent company of Schuler, has elevated battery production for the electromobility sector with a total of seven growth projects. The goal: help battery makers produce competitive batteries in Europe and America.
The first step was the acquisition of the Italian Sovema Group in August 2022. In the automotive sector, Sovema made a name for itself over the past ten years as a system supplier for pilot and laboratory projects in the field of lithium-ion batteries. In addition, the company is considered a leading global provider of turnkey systems for the mass production of lead-acid batteries. The US subsidiary Bitrode also contributes additional equipment and know-how in the field of electrical battery testing of cells, modules, and packs.
With Sovema’s expertise and experience, Schuler is able to cover the entire production line in the cell assembly and cell finishing areas: the notching and stacking processes, production of housing components, and filling of electrolytes from formation to ageing to final sealing.
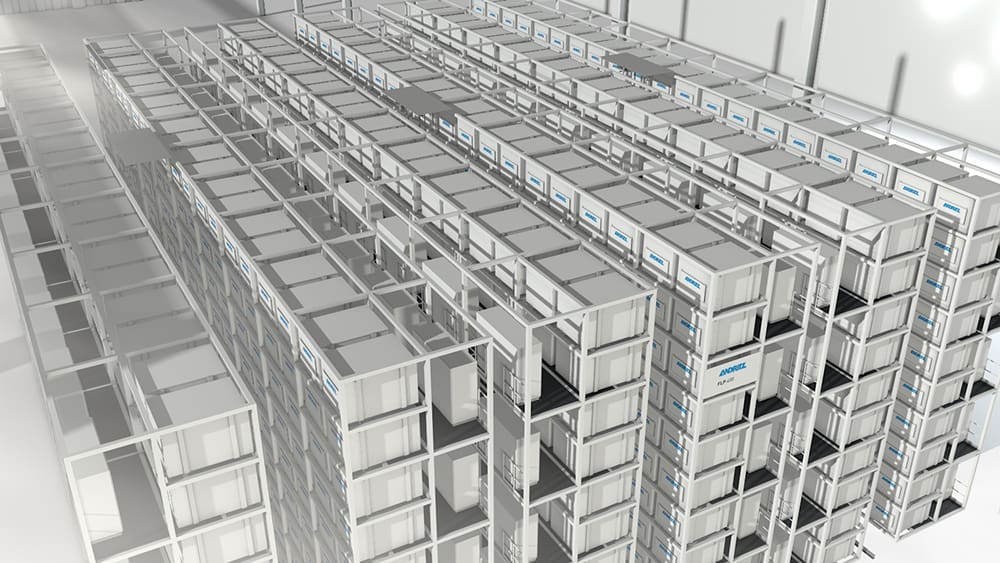
Schuler can expand the assembly and formation production lines and scale them up for the mass production of battery cells. Before the takeover, Sovema primarily manufactured laboratory and pilot systems.
In terms of process technology, Schuler can draw on its own expertise in the production of prismatic and cylindrical battery cell housings (“Can & Lid Production”), for which it has been building plants since 2015. In the field of cylindrical cell housings, the Göppingen-based company recently delivered four fully automated turnkey production lines for a world-renowned carmaker in Germany and the USA. Another line for the production of prismatic housings, with a production speed of 100 housings per minute, went to Hungary.
Expertise and capacities from other business areas of the ANDRITZ Group are available. For example, the group has been manufacturing centrifuges for lithium mining since the 1960s and also offers filter and drying systems that are needed in powder processing for the production of active cathode material. ANDRITZ also has extensive know-how in calendering processes, where rolls are used. Last, but not least, ANDRITZ’s own recycling division contributes extensive knowledge and experience in the areas of dismantling, deep discharge, and recycling of batteries. The focus here is on developments over the next five to ten years, when increasing sales figures will mean that more and more production waste from used electric vehicles will have to be recycled.
In November 2022, Schuler received an order from the Fraunhofer Research Institution for Battery Cell Manufacturing FFB at its Münster site to design a cell assembly line for large-format pouch cells in three different lengths. Another major project is currently underway for one of Germany’s major automotive manufacturers. The focus of this project is the construction of a pilot cell assembly line for the production of innovative “solid-state” battery cells. Compared to conventional lithium-ion batteries, these solid-state cells have a number of market-relevant advantages. These advantages relate to important safety aspects (unlike lithium-ion batteries, solid-state batteries cannot catch fire); they have higher energy density than lithium-ion batteries and can generate a significantly greater range for electric vehicles. Shorter charging times are another essential advantage when it comes to meeting the most demanding requirements in the field of electromobility. The turnkey handover of the plant for this major project is scheduled for May 2025.
Dr. Hermann Uchtmann, Head of Schuler’s “Battery Giga Projects” business unit, notes the reasons behind current market restraints for plant manufacturers in the field of battery production: “Taking the current sales figures for electric cars as a starting point, the battery market for automotive applications is in a phase where the exaggerated expectations have arrived in the ‘trough of disillusionment.’ We expect demand to pick up significantly again in the coming years. We are using the time effectively to optimize our products for gigafactory lines in the area of battery cell production for market demand.”
But to what extent can Schuler capture the market share from competitors in the Far East? For those in charge, the most powerful arguments here are directly linked to the core concepts of innovation, quality, and efficiency. Uchtmann states: “In the future, we want to make greater use of our innovative edge in the field of plant technology, particularly in the area of large-scale production. This is relevant for a target group, such as the automotive sector, which places the highest demands on production. This is how we can combine our outstanding quality features and the special cost-effectiveness of our systems into a common denominator.”
In battery cell production, the high manufacturing quality is reflected, above all, in low rejection rates. Another important factor, especially for the German market, is the lowest possible energy consumption that is measured against the consumption values of competitors. Uchtmann says: “Here, for example, we can achieve high energy efficiency values of almost 90 percent using the formation electronics we employ.” According to Uchtmann, further savings can be made by minimizing the space required, especially where high costs can arise for the operator—such as operating drying rooms.
For Uchtmann, the services that accompany the plant construction clearly speak “pro Schuler.” “A decisive advantage is that our plants are predestined for use in the European market. Unlike in Asia, European battery cell manufacturers are accustomed to having their plants delivered, assembled on-site, and set up ready for operation. Added to this are the reliable maintenance and repair services that we provide in the after-sales sector, including highly reliable spare parts deliveries. It is here, in the continued productivity and availability of the plant, that our expertise really pays off: the customer then has a partner at their side that they can rely on!”
Learn more at www.schulergroup.com.