The development of electric machines has evolved significantly in recent years due to ever-increasing performance requirements for automotive applications such as efficiency, power density, cost, and noise. Simulation and virtual development play a crucial role in reducing development time, cost, and risk to achieve these performance goals.
In this webinar at our Spring Virtual Conference on EV Engineering, presented by Ansys, we will demonstrate virtual solutions to key challenges faced in modern electric traction motor design and introduce the class-leading virtual development platform for electric motors.
Other sessions at our Spring Virtual Conference include:
Data-Driven Decision Making To Reduce Downtime And Risk While Improving Productivity In Your Automotive Plant
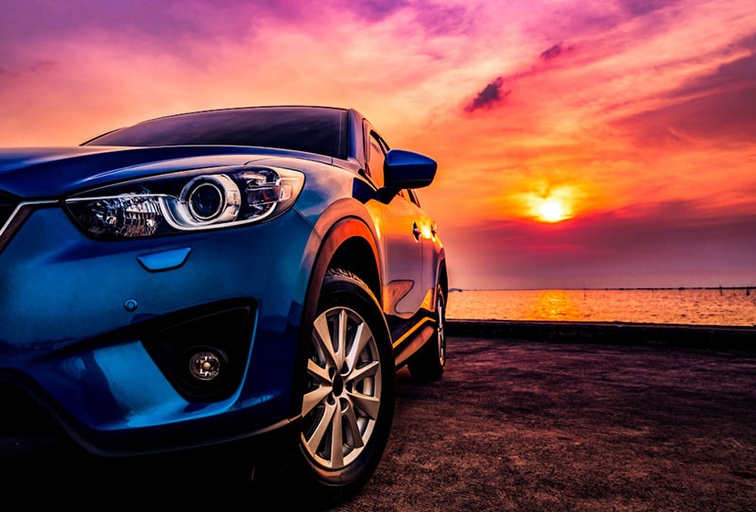
As the electric vehicle industry continues to expand exponentially, established players and newcomers alike are looking for easy-to-use and effective solutions for maintenance and quality. This means manufacturers are exploring opportunities to digitize areas like maintenance by using computerized maintenance management systems (CMMS) to track and predict asset lifecycles. And as we work to bring more EVs to market at a faster-than-ever pace, driving predictable and repeatable product quality is essential to success and safety.
In a remote, hybrid, and distributed world, cloud-based applications give teams access to essential information and workflows that improve productivity and uptime.
In this session, we will cover the trends we’re seeing with management software and share the massive potential that exists in the automation space.
Other sessions at our Spring Virtual Conference include:
Using Artificial Intelligence To Inspect Batteries With 3D X-ray Microscopy And Computed Tomography
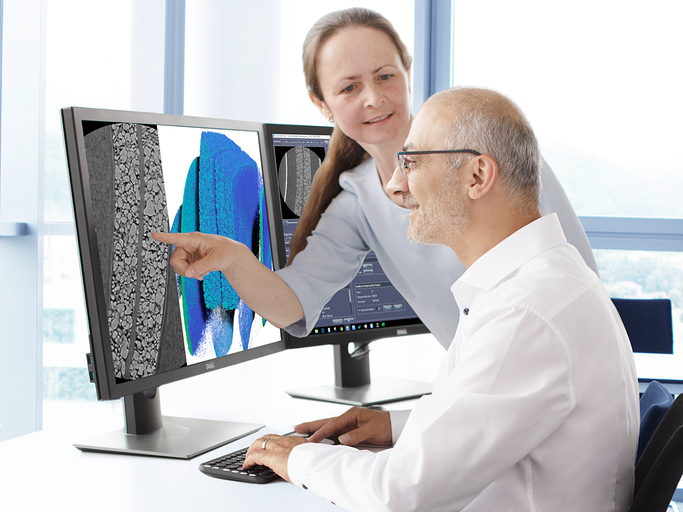
This presentation shows how to use artificial intelligence technologies to inspect batteries with 3D X-ray microscopy (XRM) and computed tomography (CT). More specifically, it illustrates how deep learning-based algorithms for CT reconstruction can be integrated into 3D X-ray inspection workflows for batteries. In addition, artificial intelligence (AI) provides a wide range of tools for automated defect recognition (ADR) of complex components that are difficult to analyze using traditional measurement methods. Machine learning (ML) platforms can train ADR models to assess battery overhang and inclusions. In the end, using deep learning-based algorithms for CT reconstruction, such as ZEISS DeepRecon, allows for 3D XRM workflows to be applied much more economically by reducing the time required for data acquisition. ML for defect detection provides a wide range of tools that can increase accuracy of detection and allow for ADR to work on lower quality (faster) CT images. Artificial intelligence-based X-ray inspection technologies will have a major impact on testing and failure analysis of batteries where non-destructive imaging is often required.
See the full session list for the Spring Virtual Conference on EV Engineering here.

Broadcast live April 17 – 20, 2023, the conference content will span the EV engineering supply chain and ecosystem, including motor and power electronics design and manufacturing, cell development, battery systems, testing, powertrains, thermal management, circuit protection, wire and cable, EMI/EMC and more.